The Complete Gym Setup Guide: How to Source Flooring & Equipment as One System (Not Separate Pieces
"83% of gyms with mismatched flooring/equipment face 30% higher maintenance costs (IHRSA & FIBO Joint Study 2024). Here’s the smart way to bundle."*
Introduction
"A gym floor that cracks under dropped weights. Equipment that stains your new mats. These disasters happen when you buy separately."
Combined procurement solves 3 hidden problems:
✓ Structural conflicts (e.g., rigs damaging floors)
✓ Warranty voids (e.g., equipment makers blaming floor failures)
✓ Double logistics costs
Mistake 1: Buying Flooring & Gear from Different Suppliers
❌ The Problem:
57% report "finger-pointing" when issues arise (McKinsey)
Case Study: A Berlin gym’s rig legs dented their flooring → Both suppliers denied claims
✅ The Fix:
Demand System Integration Testing
Ask for:
Vibration test videos (weights dropped on YOUR exact floor sample)
Chemical compatibility report (e.g., rubber soles vs floor coatings)
Mistake 2: Ignoring Installation Sequence
❌ The Problem:
Typical timeline waste:
Install flooring → Wait 7 days curing → Move in equipment → Scratches occur
Equipment arrives first → Can’t properly anchor → Uneven floor seams
✅ The Fix:
Optimal Installation Flow
Day | Task | Key Checkpoint |
---|---|---|
1-3 | Floor base layer | Moisture test (<2.5% RH) |
4 | Anchor heavy equipment | Laser-level alignment |
5-7 | Final floor surfacing | 48hr equipment cover protection |
Pro Tip: Insist on one project manager for both phases.
Mistake 3: Overpaying for Piecemeal Shipping
❌ The Problem:
Separate shipments cause:
42% higher freight costs
Customs delays
✅ The Fix:
Bundled Logistics Savings
Example: 40’ HQ Container Load
Flooring Only: (18 pallets, 60% space wasted)
Combo Load: (Floors + disassembled equipment, 95% utilization)
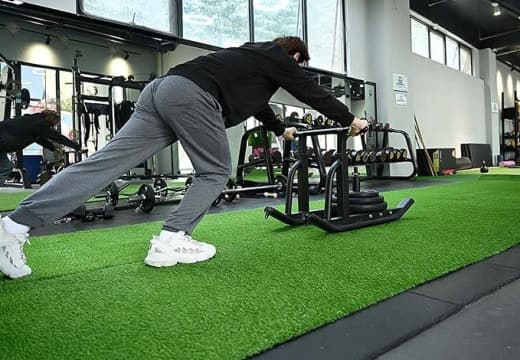
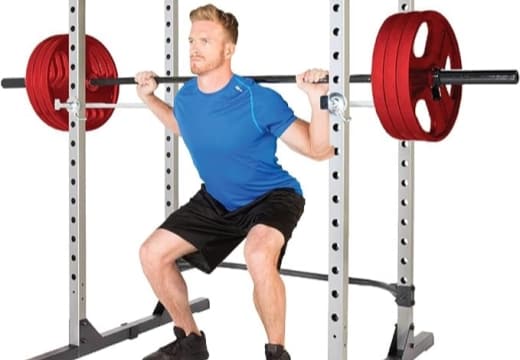
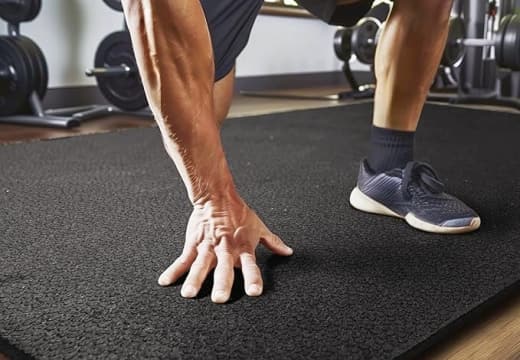